Rob Freitas is one of the best-known mould makers in the industry and has a phenomenal reputation.
Not only is he incredibly skilled at making moulds but he has a passion for the provenance of the techniques which he uses and cares deeply to help interested parties understand so they can be better too.
He also will redirect much of the attention he gets to his predecessors and those peers whom he feels deserve more attention. It’s a very generous attitude which I believe is born out of an unabashed passion for the subject and a desire to fan those flames in others. It comes from a very pure place and it’s not often you meet someone with that much knowledge, skill and wisdom and who also is phenomenally approachable and easy to talk to. He’ll no doubt blush to read these words.
We hooked up at a pub near the Millennium FX in Aylesbury where he was teaching a class that week, and a few of us slunk off to the lobby of Rob’s hotel to talk bronze age axe heads, seamlines and technology.
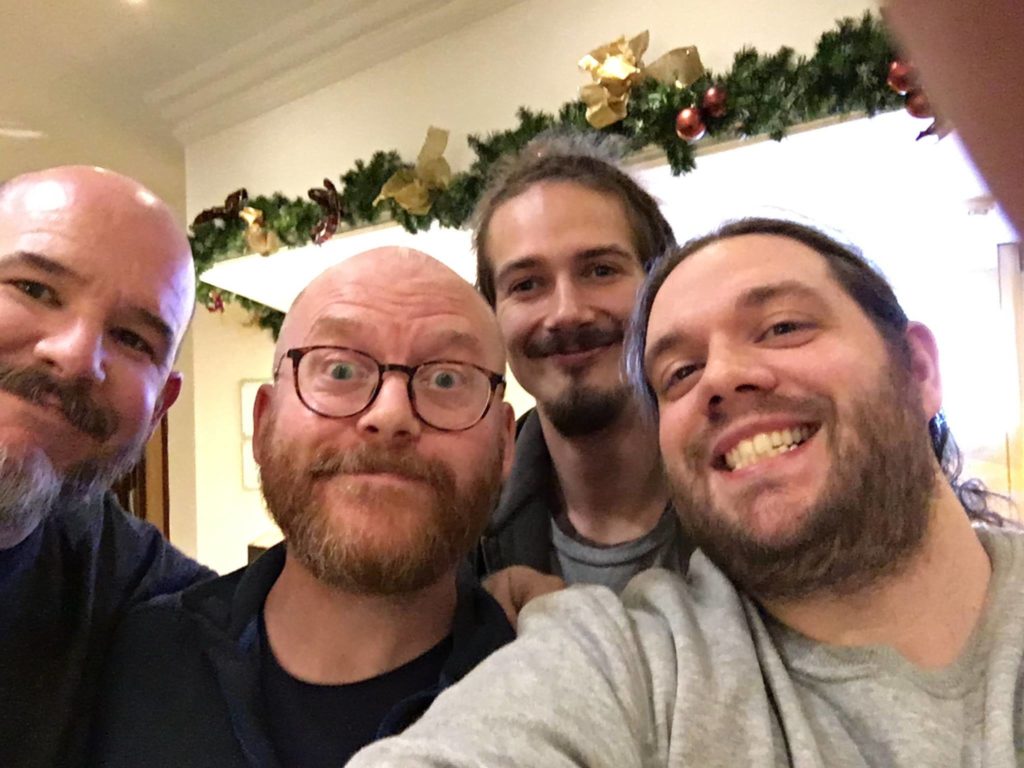
Rob, me, Ivan Bellew and Nat Reynolds. Good times!
The audio is clear, but there is some background noise owing to the nature of a public space. It was around 10pm when we started and we kept at it until around 0130…that’s how interesting it was. Just a magical few hours and I’m really pleased we could synch schedules to be able to sit down and talk.
Listen here, download or get us on iTunes, Google Play Music, Stitcher, iHeart Radio or wherever you get your podcasts!
In this first of two parts, we talk about
- Learning lessons through failure.
- The importance of looking at the past and knowing on whose shoulders we stand.
- Shortened timescales and managing expectations of people who seek to learn and gain skill (it is my belief the relatively short duration of courses as compared with time-served apprenticeships) can rob people of valuable lessons acquired through error and repetition).
- Caring about the right things in order to be better.
Axe Heads and Allies
The reason I brought that axe head was to show Rob the seams in it – evidence of moulds which have been used to make essential life sustaining tools and weapons. Moulds have been aroud for so long, and it gave me a bit of thrill to be able to have a modern day master mould maker touch a casting from an ancient mould and admire their handiwork 2500 years on.
(Incidentally, this estimation is based on a bit of research I did into bronze age artefacts. This particular head is a palstave, check out http://www.antiques-info.co.uk/new/pdf/July02/1.pdf).
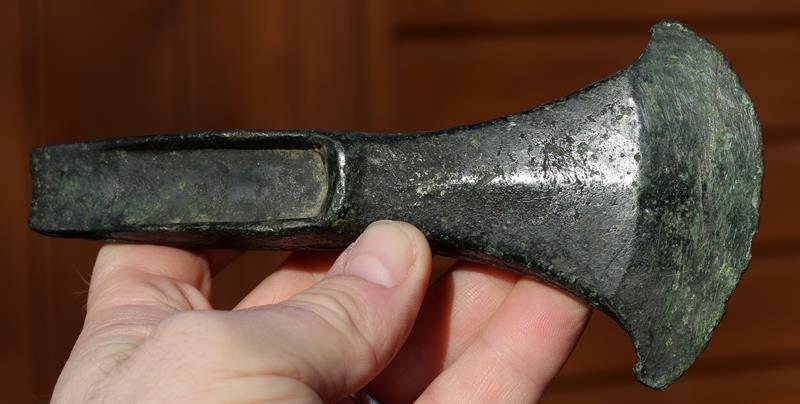
The palstave head in question.
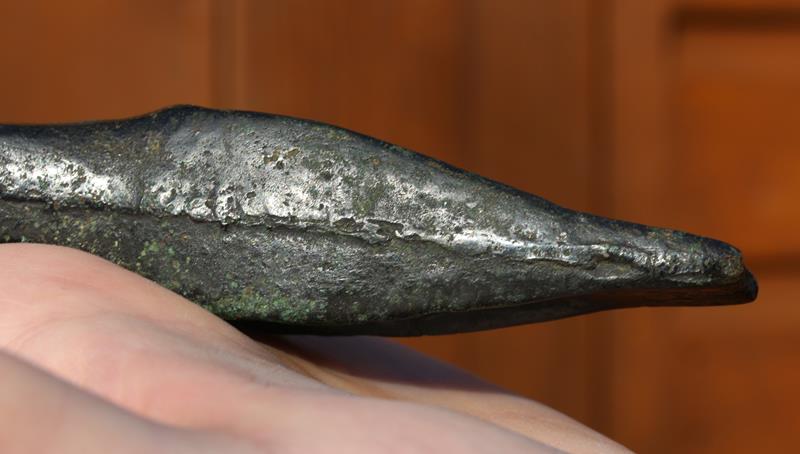
See – a seamline!
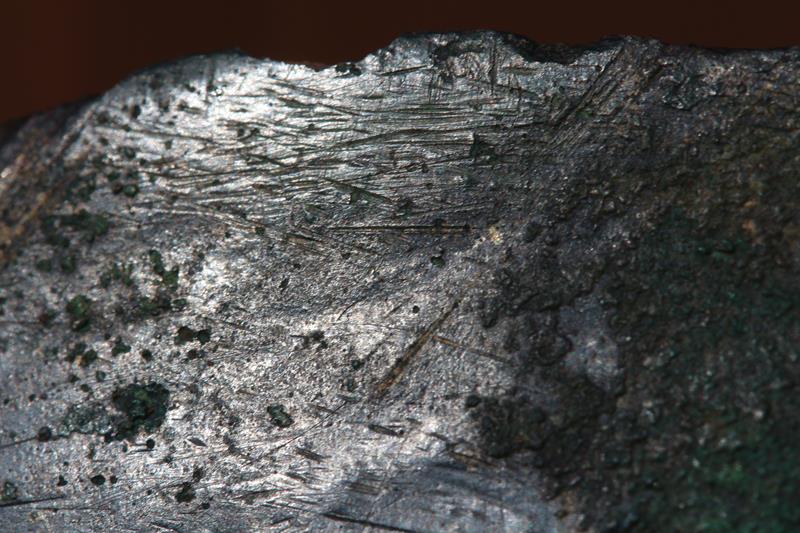
Ancient toolmarks presumably from attempts at sharpening.
This old artefact has seams, and we still face this issue in moulds today. A lot of what we do and the work involved is in overcoming the seams or minimising their impact or appearance.
In the effects world where cosmetic perfection matters, making a good mould with a great seam is important and has a dollar value later down the line! It is also one of those crafts which isn’t seen in the final images of the makeup on set, and as a result doesn’t always get the love it deserves. A great sculpt, application, design or paint job can be appreciated in person on set but the mould is nowhere to be seen.
It’s funny that even with the advent of 3D printing, stuff still often gets finished up and moulded traditionally to produce casts as it often is still the best way to make things. Mould making is such a key skill, and the abilities of those that do it well really deserve some attention.
As with learning and getting competent with practical skills, the path to success can be hampered by a desire or pressure to run when walking hasn’t been perfected. I believe the way forward is to do something small, do it well and then scale up gradually.
Videos
We mention a couple of videos that are on YouTube which show skills at work – hand making globes from 1955 (https://www.youtube.com/watch?v=4RWcWSN4HhI) and a Disney video explaining the different types of rivet (https://www.youtube.com/watch?v=IDbTUt3OG9s).
This was something Disney did to help the war effort, when training many civilians to make military equipment like aircraft required detailed explanations of manufacturing processes such as these. How better to explain these intricate and involved processes than with an animation, condensing time and showing materials in cross section.
Look out for part 2 coming very soon, and subscribe to use on iTunes, Stitcher, iHeart Radio and Google Play Music to name but a few!
Thanks,
Stuart
Really cool being a fly on the wall for that conversation,
Cheers Mr Bray!
Its about time we get to hear some words of wisdom from Rob Freitas.
really nice interview,love all of Rob’s thoughtful comments
Hey Jim – totally was an amazing experience for me.
-Stuart